Gas Thermal Mass Flow Sensor Utilizing the Bypass Concept
Abstract
This article delves into the operational intricacies of thermal gas flow meters employing the laminar flow element for precise gas flow measurement. With a focus on the working principles and applications, it highlights the significant role these flow meters play in various industrial processes, including onsite calibration setups for flow meters, hydrogen storage in metal hydrides, and control and monitoring of flow in diamond coating processes using chemical vapor deposition (CVD). Understanding the concept of the laminar flow element and its applications is crucial for accurate gas flow measurement and process control, contributing to the success of these applications.
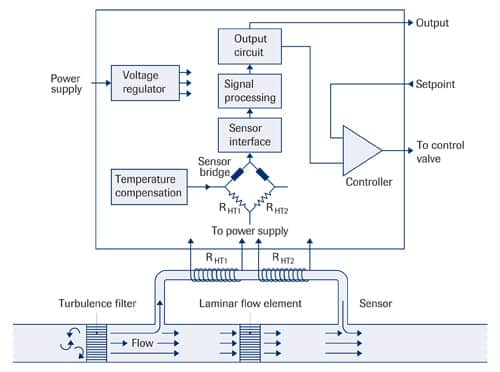
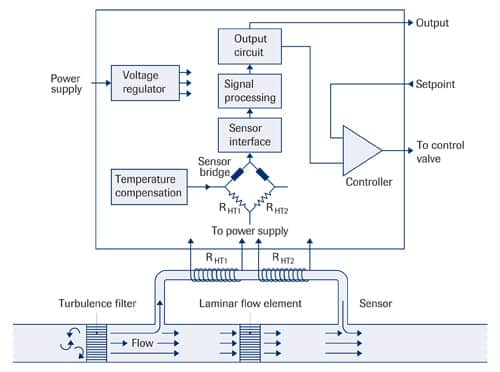
Introduction
Thermal mass flow meters are essential instruments for accurately measuring gas flow in various industrial processes. Among the various models of these flow meters, those equipped with a laminar flow element are a common choice due to their efficiency and reliability. In this article, we explore the operational details of thermal gas flow meters that utilize the laminar flow element.
Laminar Flow Element
Thermal gas flow meters that employ the laminar flow element are typically what come to mind when discussing thermal flow meters. The concept is illustrated in the figure above. In this picture, the measurement of mass flow occurs in the flow bypass, rather than the main flow channel. This sensor operates in the laminar flow regime, ensuring precise measurements.
The laminar flow element comprises a capillary tube with thin metal walls, enclosed by metal wires that both heat the tube and measure its temperature. The small diameter of the capillary tube allows for rapid response times and low energy consumption since only a small volume of the tube needs to be heated. However, a filter is necessary before the mass flow meter to prevent any blockages in the capillary tube.
The laminar flow element, located within the main flow channel, diverts a portion of the fluid into the sensor bypass, which runs parallel to the main flow channel. This element consists of a stack of stainless-steel discs with precisely etched flow channels, having similar characteristics to the flow sensor. For higher flow rates, these discs include an additional section to mitigate turbulence effects, ensuring a stable and reliable flow even under changing process conditions.
Temperature Measurement in Thermal Mass Flow Meters
When gas flows through the sensor, two heaters (R-HT1 and R-HT2 in the first figure) heat the gas. The temperature of the tube is monitored at these two points, making these heaters function as sensors. In the absence of flow, there is no temperature difference between the two points in the bypass. As flow increases, the temperature at the first measuring point (R-HT1) decreases because the fluid carries away its heat. Simultaneously, the temperature at the second measuring point (R-HT2) increases as the fluid carries heat to it. A higher flow rate results in a larger temperature difference, which is directly proportional to the mass flow.


Applications of Thermal Mass Flow Meters with Laminar Flow Element
These pass-through mass flow sensors find utility in a diverse range of applications. Their uses include onsite calibration setups for flow meters, hydrogen storage in metal hydrides, and control and monitoring of flow in diamond coating processes using chemical vapor deposition (CVD). They play a crucial role in conducting precise measurements and control in these processes.
Conclusion
Thermal mass flow meters with a laminar flow element play a fundamental role in various industrial processes, ensuring accurate gas flow measurement and control. Understanding their operational principles and applications is of paramount importance for optimizing performance in these processes. To succeed in executing these processes, mass flow meters with a laminar flow element provide the required precision and reliability.